As awareness of climate change increases, so does the focus on the concrete industry and the contribution it makes to GHG emissions. At this point it is worth noting that it is the cement manufacturing that contributes the most towards emissions associated with concrete and not the concrete itself, concrete being a composite material. A point that is sometimes lost on some. Undoubtedly, we need to reduce the emissions before it becomes too late, by 2030, but we cannot wait for new and emerging cement technologies to achieve this, we should first adapt existing cement technology and improve our own understanding of how we can use it to reduce the impact of concrete construction whilst maintaining and delivering future infrastructure projects and other developments. This means being a little smarter with OPC (ordinary Portland cement).
1. What is Low Carbon Concrete?Â
 There is no clear definition for what a low carbon concrete is, or certainly no value prescribed for the embodied carbon that would qualify a concrete as ‘low carbon’, so maybe we should be using the term ‘lower carbon concrete’ when we are discussing this issue. For example, using a blended cement with GGBS, PFA or even lime, will always reduce the embodied carbon footprint of a concrete mix design than if we simply used CEMI. When we think about or discuss low carbon concrete, we automatically turn to novel cements, AACM’s and geopolymer concretes. But they can only be considered as a viable option to the existing cement technology, if they work, are suitable, cost effective and are used in the appropriate application, otherwise, they become unsustainable and anything other than low carbon concrete or a benefit, very quickly!Â
2. Existing TechnologyÂ
 1. Summary for Policymakers of IPCC Special Report on Global Warming of 1.5°C approved by governments – https://www.ipcc.ch/2018/10/08/summary-for-policymakers-of-ipcc-special-report-on-global-warming-of-1-5c-approved-by-governments/Â
2. 5th Edition, Peter C Hewlett and Martin Liska, Chapter 17Â
3. Alkali-activated cementitious material (AACM)
Concrete made from ordinary Portland cement and/or combinations, can be classed as lower carbon concrete if we are a little cleverer with our mix designs and are prepared to think about what it is that we intend to build. A great example of this point is covered in Leas’s Chemistry of Cement and Concrete2. In some cases, by increasing the amount of cement in a concrete mix, which makes the recipe stronger, can result in the elements reduction in size and total volume of concrete.
This all leads to a total reduced cement and aggregates used and of course, fewer deliveries. Each concrete batch may have a higher carbon footprint, but the finished 75MPa element, as in the example above, has a significantly reduced carbon footprint in comparison to the 25MPa alternative and as such, can be considered as a ‘lwer carbon concrete’.
Alternatively, reducing the CEMI content and increasing the SCM will, unsurprisingly, produce a lower carbon concrete. Our own research carried out in 2017, commissioned by Keltbray Piling and with the assistance of Jack Sindhu (Capital Concrete) and BASF, a number of mixes satisfying DC classes 2-4 with a range of blends (30:70, 25:75, 20:80) were batched and assessed for strength development of C32/40 and carbon values, given a standard CIIIA (50:50) has a carbon value of 189kg/m3. From the results in Fig 2 below, we can see that the specified strength was achieved for the three mixes within the required period with enough margin attained for production control.Â
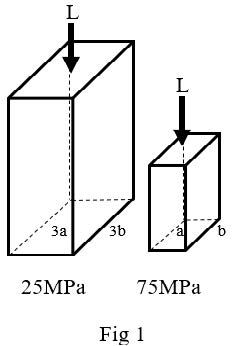
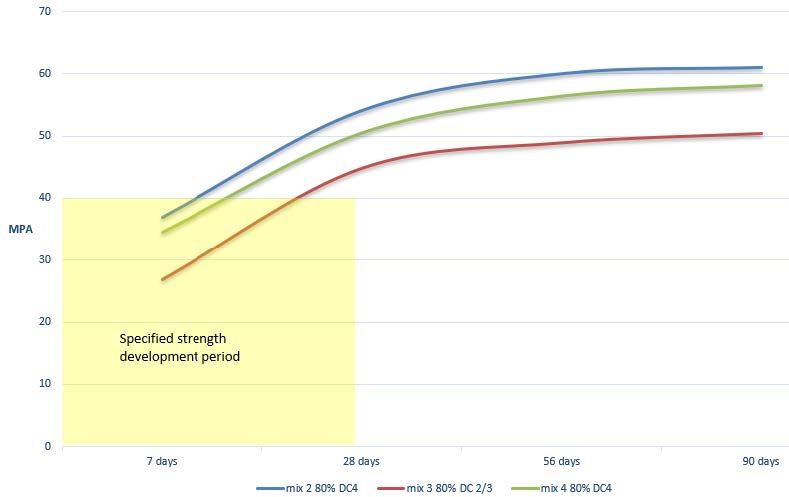
 All three piling mixes have an embodied carbon footprint of <100kg/m3, which represents a significant reduction, by simply applying a strict w/c ratio and utilising effective admixtures.Â
Extending the strength development period to 56 days would present an opportunity to revise the mixes from a CIIIB to a CIIIC, reducing the carbon value further, but maintaining the strength at the time it is required. It is so often the case that piling concrete is over specified in terms of strength development. Quite simply, why do we specify a C32/40 at 28 days, when the pile, in most cases, will not be loaded for 90 days or more? Because we have always done that!Â
3. New TechnologyÂ
 As with any industry, technology is continually advancing, and the concrete or cement industry is no different. Over the last few years, manufacturers of AACM’s3 and Geoploymers that claim to offer a real alternative to common cements have come to the fore, particularly on the back of the social movement on climate change. Despite the assertion that a real alternative to a CEMI concrete is available in the UK, the take up of these ‘novel cements’ has been slow and may even be stalling, despite the appetite for them remaining strong.Â
There are a number of factors at play here which currently impede the progress of full-scale adoption for AACM’s and/or Geoplymers, not least of which is the maturity of the technology. Common perceived barriers to acceptance of AACM’s4 include the following:Â
- Existing codes and standards
- Cost of the technologyÂ
- Suitability or Technology Readiness Levels [TRL]Â
 3.1. Existing Codes and StandardsÂ
Manufacturers of AACM’s may view the existing suite of codes and standards as a major barrier to bringing the new technology to market. It is true that BS EN 197 does not detail AACM’s as a common cement and only describes the composition of clinker cements (27 in total). It is also true that BS 8500 part 1 and 2 only provide guidance on the method for specifying and the materials for concrete, that are all clinker based. However, with the absence of inclusion in the current suite of codes and standards, AACM manufacturers could possibly rely upon code compliance by following the guidance provided in Eurocode – Basis of Structural Design ( BS EN 1990:2002 cl 5.2 “Design assisted by testing” & Annex D, cl D3.1b [material properties] & D3.1d [confirm elements/systems perform as expected]. Engineers or manufacturers who want to specify an AACM may also decide to complete tests in accordance with cl D3.1g [confirm behaviour of as built elements].Â
The introduction of PAS 88205 is a step in the right direction for eventual approval and acceptance of AACM’s, but there is still more work required for this standard. To the un-initiated, the world of AACM’s can be quite confusing, not least due to the fact the mechanism of the activator(s). Some of these activator(s) are liquid, some are powder, some are a hybrid of both and some rely on a minor addition of CEMI and others do not! (Still with us?)Â
Comparing AACM technology with well established current cement technology may be presenting a barrier, rather than the existing codes themselves. In order for AACM’s to be incorporated into any future code revisions, significantly more information such as the formulations, test data and evidence needs to be provided and assessed, which, surprisingly some of the UK manufacturers appear to be reluctant to do.Â
Rather than lobby for inclusion into existing codes, maybe AACM manufacturers would be better served in developing a new British Standard, equal to those that exist today for clinker cement (just a suggestion!).Â
With the exception to High Performance Concrete, cost is one of the foremost considerations for any Project, if not the primary factor when selecting and procuring concrete materials in terms of performance and the prevailing environment of the service life of the structure. In order to be competitive with standard concretes, an AACM will need to be at least within 15% of a comparable OPC mix, unless of course the AACM is classed as a High-Performance Concrete [HPC]. High-performance concrete may be defined as concrete with strength and durability significantly beyond those obtained by normal means.Â
Even though there is an appetite for low carbon technology [or do we mean lower carbon technology?] someone will have to pay for it, ultimately. The cost for a m3 of AACM will be sensitive to the manufacturing process which includes blending in some cases, infrastructure adaptions and may well be dependent upon the geographical location of the batching plant in terms of distance from the manufacturing plant. The assumption or claim that AACM’s fit well with the existing batching infrastructure is stretching reality a little. For powder activators, a batching plant will need to have a spare silo or be prepared to sacrifice one that is being used to stock other powder. Alternatively, and if space allows, have a new silo dedicated to AACM powder installed. For liquid-based activators the same principle exists, but instead of a silo, a dispensing unit would need to be installed. Some may view these adaptions as a small price to pay, but basic economics would call for a balance in the investment against the demand levels for the technology.Â
3.3. Technology Readiness LevelsÂ
Any research and development [R&D] must be able to measure its own progress to market readiness, using the principle of Technology Readiness Levels6. If the technology is measured at stage 3, then it is not ready for the market, if it is at stage 6, then like before, it is not ready for the market. IfÂ
Fig 3
Â
the technology is measured at 7 or 8, then it is close, but not quite ready! What ever AACM technology is considered and for whatever application, especially permanent works, then that specific technology has to be measured as 9.Â
We would suggest that once an AACM technology is assessed as being at stage 9, then that is the time for consideration of inclusion into a British Standard or the development of a new standard specific for AACM’s, as shown in Fig 3. Based on that premise, existing codes and standards do not present a barrier to the use of AACM’s. Moreover, if an AACM is at TRL 9, the information and test data that would be reviewed for inclusion in an existing code or for inclusion in an alternative and specific code for AACM’s, could and should be used to navigate the time required to publish a revised or new standard, by taking the route provided by BS EN 1990:2002 cl 5.2 “Design assisted by testing”, in the interim.
Commercial Enterprises are understandably keen to see and experience interest resulting in the use of their technologies, after all, the sales they make will help recover any investments made. The pressure to recuperate the cost of development though must be tempered by the time required to develop and prove the technology. Sentiment and/or political or social will is not enough to advance AACM technology regardless of the GHG emissions levels. Advancement of AACM’s can only be achieved by rigorous testing and provision of evidence that the technology is fit for purpose.Â
4. ConclusionsÂ
There is no doubt that AACM and geopolymer technologies will have a huge part to play in reducing the carbon footprint for Projects in the not too distant future, as well as providing additional durability benefit for concrete elements. However, we should not be waiting for this perceived ‘silver bullet’ but utilise the existing cement technology now, to minimise the impact that construction activities are having, and which are contributing towards GHG emissions. Clients and engineers are best placed to drive innovation from existing cement technology by replacing prescriptive specifications with hybrid performance specifications that require some carbon reduction targets. This would encourage contractors (who are ultimately defined as the specifiers8) to work with the concrete producer to develop mix designs that not only satisfy any mechanical and durability requirements, but also encourage the use of lower carbon concrete.Â
It remains the responsibility of the AACM manufacturers to demonstrate that their technologies are suitable and ‘fit for purpose’, but this process may take considerable time to evidence and may come too late to have any positive benefit on reducing carbon emissions by 2030. The investment, dedication and sheer tenacity that is often required to bring new technologies to market may be too much for some commercial enterprises, especially if the industry suffers any long term slow down, as we seem to be experiencing at this moment.
As we should not be waiting for the development of suitable AACM’s, manufacturers who have reached a TRL 9 level should not be waiting for a revision or new publication of a British Standard, a route does exist to utilise proven and robust AACM technology, in which case, the ‘silver bullet’ should be loaded and fired!!Â